Recognizing What is Porosity in Welding: Reasons and Solutions
Porosity in Welding: Identifying Common Issues and Implementing Best Practices for Prevention
Porosity in welding is a prevalent concern that commonly goes undetected up until it causes substantial issues with the stability of welds. In this discussion, we will certainly explore the vital factors adding to porosity development, analyze its destructive impacts on weld performance, and go over the best methods that can be adopted to reduce porosity occurrence in welding procedures.
Common Root Causes Of Porosity

An additional constant wrongdoer behind porosity is the visibility of pollutants on the surface area of the base metal, such as oil, grease, or corrosion. When these contaminants are not successfully gotten rid of before welding, they can vaporize and end up being trapped in the weld, causing flaws. Moreover, using unclean or damp filler products can present pollutants right into the weld, adding to porosity concerns. To minimize these typical root causes of porosity, thorough cleaning of base metals, appropriate securing gas selection, and adherence to optimum welding criteria are essential methods in achieving high-grade, porosity-free welds.
Influence of Porosity on Weld Quality

The visibility of porosity in welding can substantially jeopardize the structural integrity and mechanical properties of welded joints. Porosity develops spaces within the weld steel, deteriorating its overall stamina and load-bearing capability. These voids serve as stress and anxiety focus points, making the weld more susceptible to breaking and failure under used lots. Furthermore, porosity can minimize the weld's resistance to rust and various other ecological elements, additionally reducing its long life and performance.
Welds with high porosity degrees have a tendency to exhibit lower effect toughness and decreased capability to deform plastically prior to click here for info fracturing. Porosity can hamper the weld's ability to effectively transmit forces, leading to early weld failure and potential security threats in crucial frameworks.
Best Practices for Porosity Prevention
To boost the architectural integrity and top quality of welded joints, what certain procedures can be carried out to decrease the occurrence of porosity during the welding process? Using the right welding strategy for the specific product being welded, such as changing the welding angle and gun placement, can better prevent porosity. Routine inspection of welds and prompt removal of any concerns recognized throughout the welding process are vital methods to prevent porosity and generate high-quality welds.
Value of Correct Welding Techniques
Applying appropriate welding strategies is extremely important in ensuring the architectural integrity and quality of check this site out bonded joints, constructing upon the foundation of efficient porosity avoidance steps. Too much heat can lead to increased porosity due to the entrapment of gases in the weld swimming pool. Additionally, using the suitable welding specifications, such as voltage, current, and take a trip rate, is important for attaining audio welds with minimal porosity.
Moreover, the choice of welding process, whether it be MIG, TIG, or stick welding, ought to align with the details needs of the task to make sure ideal outcomes. Proper cleansing and prep work of the base steel, as well as choosing the ideal filler material, are additionally important components of skillful welding strategies. By sticking to these ideal techniques, welders can decrease the danger have a peek at this site of porosity development and produce high-quality, structurally sound welds.
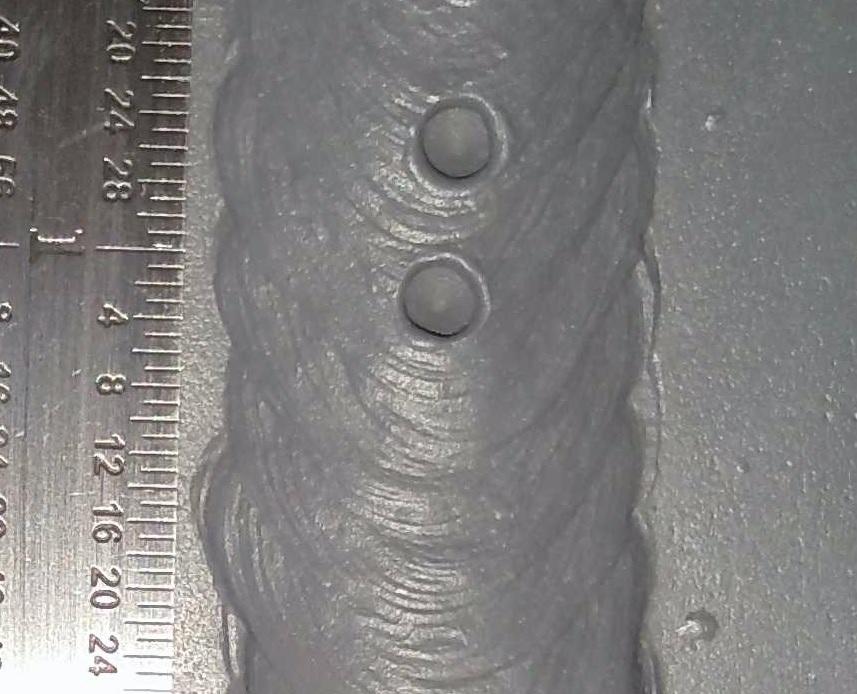
Checking and Quality Assurance Measures
Quality assurance procedures play an important role in confirming the honesty and dependability of bonded joints. Examining treatments are necessary to detect and stop porosity in welding, guaranteeing the toughness and longevity of the last product. Non-destructive testing approaches such as ultrasonic screening, radiographic screening, and aesthetic evaluation are typically employed to identify possible flaws like porosity. These strategies permit the analysis of weld quality without jeopardizing the honesty of the joint. What is Porosity.
Post-weld examinations, on the other hand, analyze the last weld for any problems, including porosity, and verify that it fulfills specified requirements. Applying a comprehensive top quality control strategy that includes extensive screening treatments and examinations is vital to reducing porosity issues and making certain the general quality of welded joints.
Verdict
In final thought, porosity in welding can be a common problem that affects the high quality of welds. By identifying the typical sources of porosity and implementing ideal practices for prevention, such as appropriate welding techniques and testing procedures, welders can make sure excellent quality and reliable welds. It is necessary to prioritize avoidance methods to minimize the event of porosity and preserve the integrity of welded structures.